Enhancing Safety Culture Through Toolbox Talks
What are Toolbox Talks?
Toolbox talks are informal safety meetings, usually held before or after the work day, that facilitate discussions revolving around safe work practices. These small meetings have proven to be very effective in keeping safety on the minds of workers as well as keeping skills refreshed. Typically, these meetings are held directly on the jobsite, which makes it easy to demonstrate the best safety practices for that particular job.
Toolbox talks should not be used as a replacement to mandatory safety training, but instead as a supplement to help build a stronger safety culture and reinforce the importance safety. Like any safety training, ensure that where you hold the meeting is a distraction-free-zone so that employees can focus and ask questions as needed. It is important to always document toolbox talks so that you have the capability to analyze which employees have attended meetings on certain topics. If you are not attentive to which employees are attending meetings, training courses or refresher courses their skills can decline, which can put themselves and others at risk.
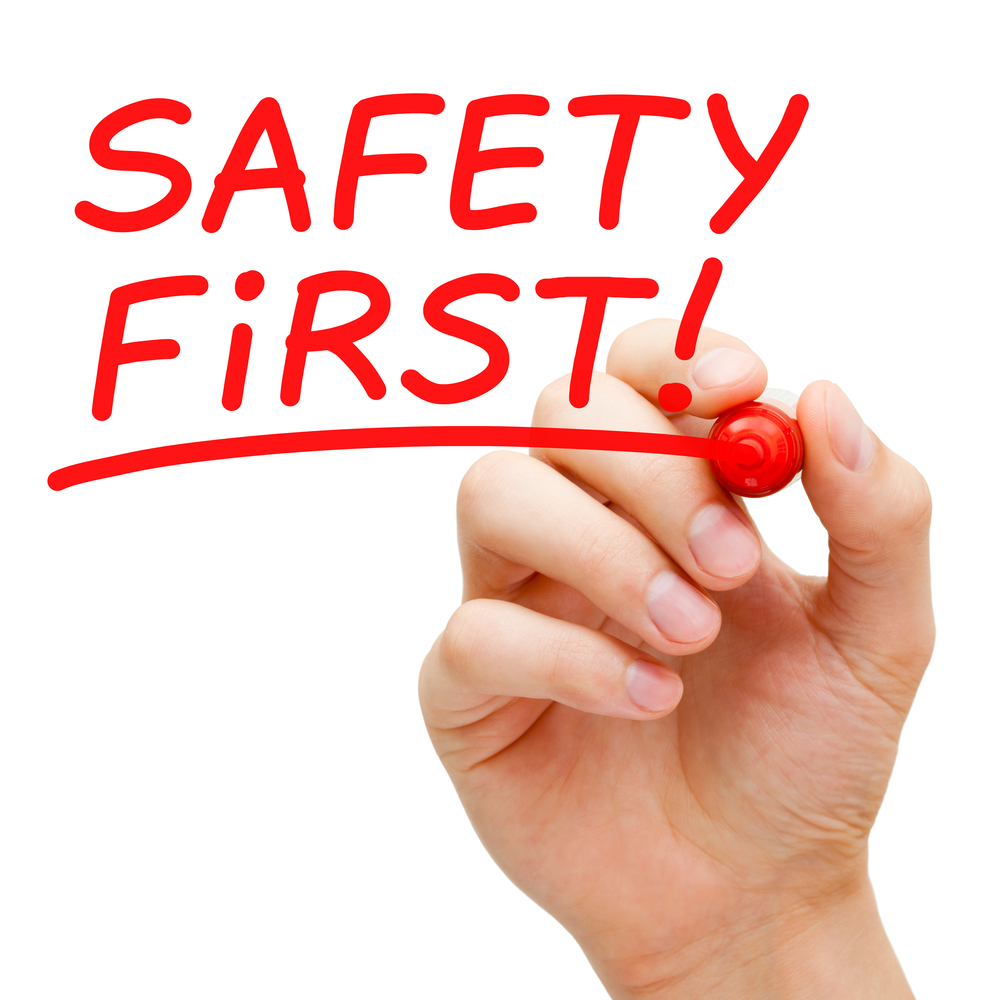
Regardless of how long someone has been doing something, it is important to keep their skills fresh and remind them of the most safe work practices. Complacent workers can cause some of the most dangerous incidents because they are too comfortable and tend to do their work mindlessly. Toolbox talks should be held on a weekly, or even daily basis if possible, to ensure that everyone on site is familiar with all safety policies and standards to be compliant with OSHA. These meetings help provide the most safe workplace for everyone on site. Make sure that each talk is centered around the most important and relevant topics on that site.
The top 5 most commonly discussed toolbox topics are:
1. Slips Trips and Falls
2. Electrical Safety
3. PPE Safety
4. Working at Heights
5. Confined Space Safety
These quick safety meetings should only last about 5-10 minutes, so be sure to have all topics organized and ready so that you can make the most of the time you have with the crew. It is important to remember when holding these meetings to highlight good work that the crew is doing to help encourage them to keep up the hard work. Getting employees involved will also help keep them engaged and help them retain the most knowledge during these meetings. Ask employees to demonstrate safe work practices or answer questions and be sure to always leave room at the end of the meeting for employees to ask questions or add helpful commentary.
There are resources to find toolbox topics online, but SMART Safety customers are provided weekly toolbox topics and content each month to help strengthen safety culture. SMART Safety also offers a wide variety of safety training and refresher courses, which include safety training cards to quickly prove that they are qualified to operate certain machinery or perform certain tasks. For more information on SMART Safety and our services, please visit our website or give us a call (844) 820-8098.
#ToolboxTalks #SafetyFirst #SMARTSafety #OSHACompliance